Label orientation system helps customer for production efficiency
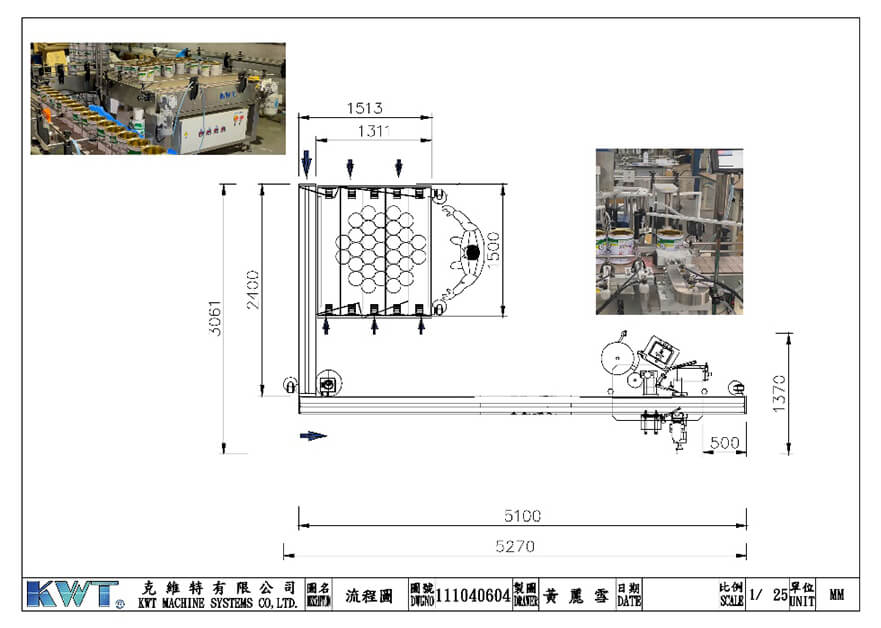
The client specializes in paint manufacturer, their lines employs a large number of workers to produce, that is hard for them to track the production, moreover, the company see a shortage of workers in the future. They are planning to invest new automatic machines step by step.
Their first labeler is semi-auto type, workers have to place the container on the required position to apply labels, after finished labeling job, collect containers by hand. Output speed depend on the worker’s speed, moreover, sometimes the label position is wrong.
In order to improve the production efficiency, KWT work with the client to find the suitable solution on their line.
- Working table for placing bulk containers and transport empty containers to the labeler.
- KWT-515 auto position wrap-around labeler with the label orientation sensor. Thanks to the orientation sensor, labels are applied on the required area. Containers are rotated by a roller while the orientation sensor detect the demand image, the labeling applicator dispatch labels on the right area, no need the worker to check the position anymore.
- Integrate the labeler into their current filling line, ensure that the line speed approach 15 pcs/min based on 1L. And reduce manual job, only one worker is able to operate.
Additionally, the main difference between the semi-auto and automatic labeler, the semi-auto relies on human operation, while an automatic only need someone to make sure that it works continually. This labeling solution improve their line efficiency and save the cost of operator labor over time.
