Bottle Rinsing Machine: A Comprehensive Guide to Cleanliness and Quality Control
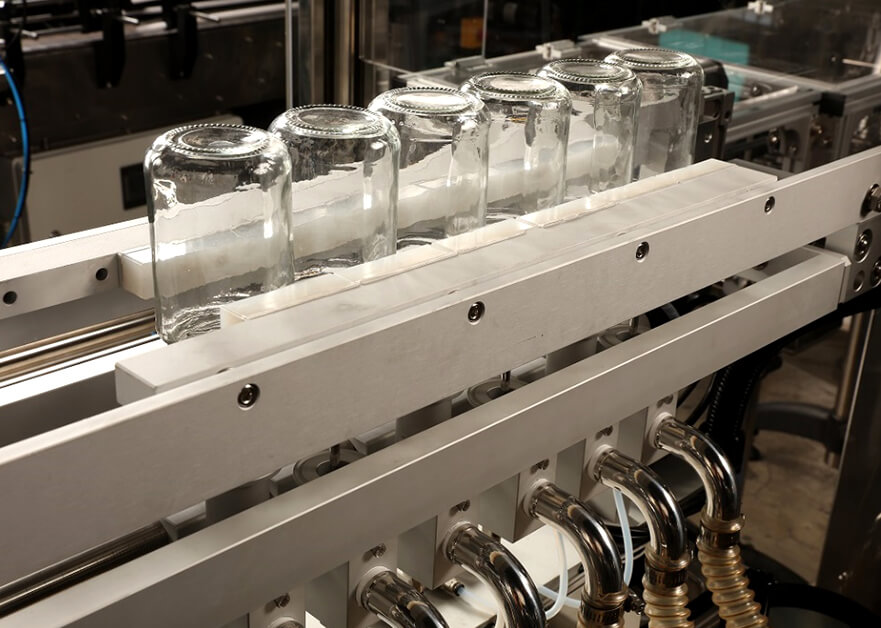
What is a Bottle Rinser?
In the bottling industry, bottle rinsers are essential for maintaining product quality and consumer safety. These specialized rinsing machines are designed to remove contaminants from containers before the filling process, creating a hygienic environment for beverages and liquid products. KWT, a professional automation and solution provider, has developed advanced bottle rinsing technologies that meet the demanding standards of modern packaging operations.
Purpose and Basic Function of Bottle Rinsers
Bottle rinsing machines are specialized equipment designed to evacuate dust, debris, and other contaminants from the inside of glass and plastic bottles before the filling process. These rinser machines make sure that containers are hygienic and clean, which is essential for preserving the flawless appearance and flavor of drinks and other liquid products. The primary purpose of these machines is to address the residue left by cardboard and other packing materials during shipment, which could otherwise contaminate the product and compromise its quality.
In industrial settings, the bottle rinsing process typically involves rotating bottles to a cleaning station where rinsing nozzles are inserted into the containers to remove debris. Bottles are rotated back to the filling line conveyor for the subsequent packaging step after being cleaned. This methodical process ensures that every container is thoroughly cleaned, leading to dependable product quality and satisfied customers.
Working Mechanisms
Modern bottle rinsers employ various cleaning mechanisms depending on the specific requirements of the product and container type. The most common cleaning systems utilize:
- Clean Air Systems: These systems use compressed air with filter to dislodge and remove dry particulate matter such as dust and packaging debris from containers.
- Liquid Washing Systems: These utilize water or specialized cleaning solutions to wash containers thoroughly, removing contaminants and potentially sanitizing the containers.
The rinsing process begins when bottles are conveyed to the rinsing station, where they are typically inverted and subjected to air or water systems to remove contaminants effectively. This inversion allows gravity to assist in the removal of debris and ensures that no residual cleaning agents remain in the container.
Technological Advancements in Bottle Rinsing
The bottle rinsing industry has seen significant technological evolution in recent years, with advancements focused on improving efficiency, reducing waste, and enhancing hygiene standards. Modern rinsing machines incorporate PLC (Programmable Logic Controller) systems with touchscreen interfaces that allow operators to store multiple programs, significantly decreasing changeover times between different container types or products.
These technological improvements have led to more efficient rinsing mechanisms that optimize water and energy usage while maintaining stringent cleanliness standards. Some advanced systems incorporate water recirculation to reduce waste, contributing to more sustainable manufacturing practices.
Design Features of Modern Rinsers
- Flexibility: Be able to use simple changeover parts to handle different container sizes and shapes.
- Versatility: Our bottle cleaner is versatile, capable of efficiently cleaning both glass and plastic bottles with ease. Designed with user convenience in mind, it delivers outstanding performance, making your cleaning process both simple and effective
- Simplicity: User-friendly interfaces that require minimal training to operate efficiently.
- Integration Capability: Easy incorporation into existing or new bottle packaging lines for seamless operation.
These features collectively ensure that modern bottle rinsers meet the demanding requirements of today's fast-paced production environments while maintaining the highest standards of container cleanliness.
The Importance of Proper Bottle Rinsing
Proper bottle rinsing is not merely a step in the production process but a critical quality control measure that directly impacts product integrity and consumer safety. Inadequate rinsing can lead to contamination issues that affect product taste, appearance, shelf life, and safety.
In industries such as food and beverage, pharmaceuticals, and chemicals, regulatory standards mandate strict hygiene protocols for packaging processes. Bottle rinsers help manufacturers comply with these standards by ensuring containers are thoroughly cleaned before filling.
Industry Applications
- Food and Beverage: Used extensively in soft drinks, water, juices, alcoholic beverages, and liquid food products packaging.
- Chemicals: Used to ensure clean containers for consumer and industrial chemicals.
- Cosmetics: Applied in the packaging of liquid personal care products where cleanliness is paramount.
About the kind of rinsing technology utilized, the cleaning agents used, and the rinsing parameters, each of these industries has particular needs.
KWT's Approach to Bottle Rinsing Technology
KWT offers several bottle rinsing solutions tailored to different industry needs:
- KWT-8W Series Water Rinsers: These machines can use water to clean bottles. They’re suitable for juices or soft drink.
- KWT-8A Series Air Rinsers: These use clean air to remove dust and debris from bottles. They’re ideal for non-liquid products like powders or capsules.
- Liner Rinsers: Depending on production needs, rotary rinsing handle high-speed operations, while inline rinsers are better for different size of bottles and easy change-over.
KWT’s rinsers come complete with conveyor systems, bottle clamping assemblies, and rinsing nozzles, all mounted on heavy-duty stainless steel frames for durability and long-term performance.
KWT has positioned itself at the forefront of this evolution, offering innovative bottle-rinsing solutions that address the diverse needs of various industries. By prioritizing design elements such as flexibility, versatility, and user-friendly, providing reliable performance while accommodating the dynamic requirements of modern manufacturing environments.
As hygiene standards continue to evolve and consumer expectations rise, the importance of effective bottle rinsing will only increase. Companies that invest in high-quality rinsing systems, such as those offered by KWT, are well-positioned to meet these challenges while maintaining efficient and profitable operations.
